In 2020, in the face of the sudden Covid-19 epidemic, Chambish Copper Smelter Limited resolutely resisted the pressure from epidemic prevention and control, managed epidemic prevention and control with one hand, and production and operation with the other hand, actively carried out the campaign of "living a tight life", comprehensively focused on "four efficiency gains", and achieved remarkable results in the areas of stable and high production, acquisition of mines, technological innovation, income increase and cost reduction. After achieving a record high copper production of 11,070 tonnes in 2019, the Company set a new record again in 2020, with an expected production of 12,800 tonnes of copper; the copper production and net profit exceeded the planned target by 28% and 19% respectively, achieving a counter-trend growth in production and efficiency.
With ores in hand, the Company is never panic. In 2020, Chambish Copper Smelter Limited adjusted its thinking on ore collection in the light of the situation, grasped the favorable opportunity and took multiple measures to enhance ore collection. 300,000 tons of ore and 8,400 tons of metal were expected to be collected this year, setting a new record for ore collection.
"Eyes inward, diligent internal cultivation, positive action and staggered development". In order to hedge against the impact of the epidemic on production and operation, Chambish Copper Smelter Limited actively carried out the "living a tight life" campaign and expected to achieve a cost reduction and efficiency increase of US$500,000 for the year, achieving 309% of the target value. Chambish Copper Smelter Limited insisted on driving development with innovation, and new achievements were also made in technical reform in various departments. The mixing and leaching workshop renewed the bottom flow pump of the thickener, which improved the operation rate of the equipment, reduced the consumption of spare parts and greatly reduced the workload of maintenance personnel; the beneficiation workshop pressed itself to fully mobilize the initiative of the Company's staff, and when the technical experts of the supplier could not come to the site to guide the installation, a commando team was formed mainly by the Company's senior technicians to complete two overhauls, namely the replacement of the semi-autogenous mill reducer and the replacement of the bushing, which were successfully carried out in one trial run. The extraction and electrowinning workshop increased the current efficiency by 5.3% and reduced the electricity consumption by 5.7% year-on-year by strengthening the management of the tank surface and installing new insulators for the anode plate to reduce the short circuit between the poles. Those small changes in technology added up to "real money" in terms of efficiency.
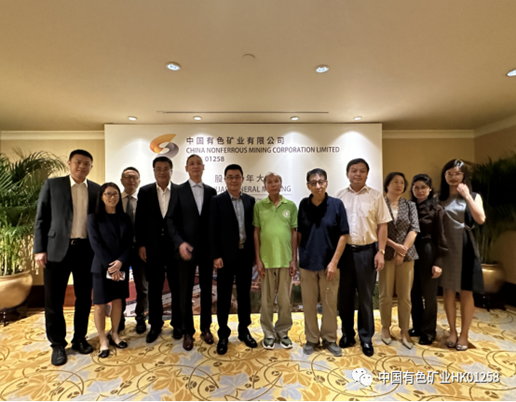