At 18:00, Dec.23, 2017, along with the discharge of the final batch of cathode copper plates, NFCA Luanshya Muliashi Smelting Plant located in Zambia and funded by the Corporation realizes the annual total output of 40,600t copper, with various economic indicators hitting the highest record, to realize the overall achievement of designed output and targets.
Muliashi Smelting Plant has a total investment of 340 million dollars, with the designed annual output of 40,000t cathode copper, being one of the largest investment projects of the Corporation. In recent years, under the constant efforts of the Plant, all employees have overcome numerous design, process and production problems in a hardworking and smart manner, to continuously optimize the process techniques and improve the output and benefits.
By overcoming technical barriers, the high-temperature agitation leaching process has been successfully applied to reward the explorers. For the Plant, raw ores are provided with a complicated nature. If the ordinary agitation leaching process is applied, the copper leaching rate is as low as 30%. According to the test, the leaching rate of copper from ores will reach 80% only when they are heated to at least 65℃. For a steam heating system with the installed capacity of 30MW, it is required to heat 12,000t ore pulp at a concentration of 50% to 65℃ each day. The steam heating system is not only an dispensable equipment for production, but also a major conflict for cost control. When the ordinary agitation leaching process is quickly applied with less cost, the agitation system of the Plant must go forward under a heavy burden. In the wet copper smelting industry, heating the ore pulp using the high-power electric boiler is yet unprecedented. Therefore, no experience or data is available, let alone any standard or code. To apply this process into the industrial operation from the “paper”, there are so many technical barriers to be surpassed, which is major issue to be solved in the trial production of the agitation system. In March 2012, the agitation system was built and put into trial run. To get through the process as soon as possible, the staff of the Plant gave up their holidays and home leaves, and they worked for 12 hours each day and undergone hardships for more than one hundred days consecutively. A number of employees got sick due to fatigue, but they returned to their work immediately upon their recovery. In 2013, the agitation system processed 1.99 million tons of ores, while the designed capacity was 1.95 million tons. Based on the smooth process, the Plant discussed the process characteristics for those complicated and hard-leaching , launched the reconstruction of a great number of process equipment, and optimized the process parameters to achieve an agitation leaching rate up to 82%. The successful application of the high-temperature agitation leaching process has set up a model for the processing of complicated and hard-leaching ores.
For the heap leaching site which was deemed as a “forbidden zone”, difficulties were removed one by one, bringing out the increasing rise of output. The heap leaching system of the Plant has the largest size in Africa. Due to the high content of ore fines, and the long rain season and annual rainfall of 1200mm, this site was once deemed as the “forbidden zone” for application of the heap leaching process. As the sprinkling production for the heap leaching system is started since 2013, the Plant has actively explored and constantly overcome issues as encountered, to make breakthroughs with respect to heaping and curing in rain season, diversion of liquid, drainage on heap surface, stabilization of side slop, and to optimize the sprinkling leaching process system and scientifically control the ore heap feeding and leaching progress, thus to coordinate the balanced production throughout the year. In such a way, the leaching period is reduced by 300 days, and the copper concentration of the leaching liquid is increased by 4g/l. Before closing of the leaching heap, the average copper leaching rate is 72.89%, while the designed rate is 72%. The copper output is quickly increased at an increment of 5000t per year, and the large-sized application of heap leaching process is initiated in Africa.
Both the output and quality of the extraction and electrodeposition are significantly improved, as a result of the rich experience and the refined management. As the production capacity is increased year by year, the quality conformity rate of the Grade-A cathode copper reaches 99% above, whist the consumption of extraction agent and solvent oil per ton of copper is lower than 50% of the average value in the industry, securing a leading position in the industry.
The planned maintenance is carried out to promote the production and development. The equipment is the physical carrier for process techniques. In many years, the Plant has vigorously promoted the improvement and optimization of process equipment and fully executed the planned maintenance. In 2017, the availability rate of the agitation leaching system reaches 93%,and that of the crushing & screening system equipment reaches 82%, higher than the design rates by 3% and 15% respectively, thus laying a solid foundation for the Plant to break through the ore processing capacity of 4.6 million tons in the year (the design capacity is 4.5 million tons) .
The concept of “Safety first” has been deeply implemented in every aspect of the production management. Due to the complicated working environment of the Plant, a lot of flammable and explosive substances and hazardous chemicals are used in the production, and the potential risk sources are distributed throughout the plant, which require a high responsibility for safety and environmental protection. In the past years, the Plant has always adhered to the safety principle of “Safety first, prevention first” and strictly executed various work safety regulations and requirements. It has created and completed various special emergency response and inspection systems, strengthened the routine inspection and the elimination of hidden hazards, defined the time limits and responsibilities related to the safety work, and set down distinctive rules for reward and punishment Since the Plant is put into operation, it has maintained a good record with its absence of major safety accident and environmental accident.
Stay true to the mission taken up, and strive ahead. In 2017, the Plant has made a lot of efforts to improve the quality and efficiency, turn losses and get rid of difficulties, thus realizing rich achievements in both output and benefits, with the cost per ton of copper reduced by 249 dollars. More specifically, the acid consumption per ton of copper is reduced by 0.74t, and the electricity consumption per ton of copper is reduced by 14%, with the profits hitting the highest record since the establishment of the Plant.
(Source: Muliashi Wet Smelting Plant)
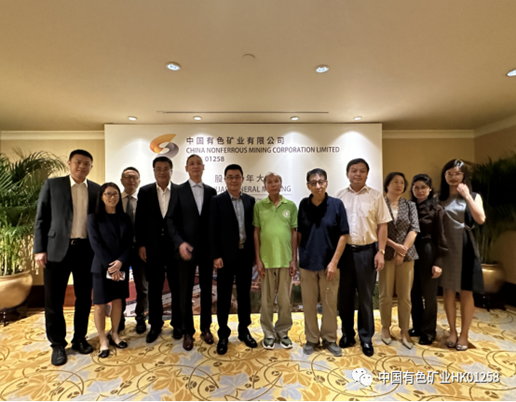