Active Adaption to Innovation and Upgradation, Exact Target at Problem Guide
23 May 2016
In the process of production, management and construction, chambishi copper smelting has achieved fantastic results in short construction period, advanced technical indicators as well as good management performance respectively. From 2015 to 2016, facing challenges in world economic slowdown and lingering weakness of copper and sulfuric acid price, the management team of CCS has made in time efforts by itself. Under the leadership of board of directors, it has deeply realized the significant meaning of the tough fight with quality and efficiency advancing; planning in advance to proactively adapt to the market; focusing on structural adjustment and management innovation to realize timely transformation and upgrading of corporate profit pattern; problem oriented, crux focused, exact target at management; billboard management, daily clearance and balance, rapid accomplishment for those who accumulate from tiny points; core leadership, same purpose between leaders and subordinates, full play to the powerful guarantee role from overseas Party construction and ideological and political work to explore a path for quality and efficiency advancing in competition benefit mode.
1.Actively adapt to new normal of regional market, carry out strictly structural adjustment and management innovation, and realize timely transformation and upgrading of corporate profit pattern. With strong fluctuation on international bulk stock price, copper price fell 20% year on year, reaching the lowest level in 6 years. This discouraged copper miners at upstream of Congo-Zambia area and sulfuric acid users at downstream on their production enthusiasm. In 2015, some mines and hydrometallurgy factories even stopped production, leading to tension supply on copper concentrate and sharp decrease on processing charges; at the same time, sulfuric acid products entered into poor market and were stocked, both failing in sales volume and price of sulfuric acid with 25% year-on-year price decrease. Facing unprecedented crises and challenges, in order to ensure the sustainable development of the company, the leader group proposed the following ideas based on calm and objective analysis of current market situation: actively adapt to new normal of regional market; implement transformation and adjustment in time and rebuild strategic position; further strengthen company core competitiveness through advancing quality and efficiency to ensure regional competition advantage.
1.Actively adapt to new normal of regional market, carry out strictly structural adjustment and management innovation, and realize timely transformation and upgrading of corporate profit pattern. With strong fluctuation on international bulk stock price, copper price fell 20% year on year, reaching the lowest level in 6 years. This discouraged copper miners at upstream of Congo-Zambia area and sulfuric acid users at downstream on their production enthusiasm. In 2015, some mines and hydrometallurgy factories even stopped production, leading to tension supply on copper concentrate and sharp decrease on processing charges; at the same time, sulfuric acid products entered into poor market and were stocked, both failing in sales volume and price of sulfuric acid with 25% year-on-year price decrease. Facing unprecedented crises and challenges, in order to ensure the sustainable development of the company, the leader group proposed the following ideas based on calm and objective analysis of current market situation: actively adapt to new normal of regional market; implement transformation and adjustment in time and rebuild strategic position; further strengthen company core competitiveness through advancing quality and efficiency to ensure regional competition advantage.
First of all, summarize the past successful profit mode; make full use of company existing regional advantage, productivity advantage, product positioning advantage and capital storage advantage; consolidate foundation and succeed before fight; secondly, actively adapt to regional market changes, take the initiative and advance& retreat in a proper degree. On one side, increase competitiveness of raw material purchase, CCS being far ahead in production ratio among four copper smelting factories in Zambia; on the other hand, enhance cross-regional cooperation and increase sulfuric acid sales, to build up complete chain of sulfuric acid storage & transportation and distribution channel of CCS in Congo; establish all in one marketing system of Zambia and Congo area; break “sulfuric acid decides productivity” pattern; what’s more, strengthen capital budget management; tremendously decrease the occupation of value added tax rebates; strictly control exchange risk. On the basis of the inheritance of past “scale economies mode”, further promote the transformation and adjustment of “competitiveness benefit mode”; for the whole value process composed by supply chain, production operation chain, sales chain and capital chain, rapid link as “the leading company” through sales by production; value exploration and optimization &integration again; build “supply chain third profit source”; realize the transformation from single track profit to multiple tracks of profit; “resource, internationalization and high end”, actively explore the expansion from single product profit to capital operation mode.
2. Problem oriented, crux focused, exact target at management; establish and complete the budget performance assessment whole value process. After deciding profit mode, in the real operation process of advancing quality and efficiency, CCS focused on enterprise major risk point and benefit “loss point” with “problem-oriented thinking”, setting bottom line, defining red line, comprehensively managing security, marketing and finance process and implementing “benchmarking management”: benchmark homogeneity index with leading index both in China and abroad; benchmark non-homogeneity index with its best level in history; find out the gap, establish goals and make continuous improvement! CCS encourages departments and branch workshops to combine benchmarking management result with information technology, make in time summarization, solidify and realize the transformation from “tacit knowledge” to “explicit knowledge”; CCS carries out budget performance assessment system under the guidance of capital & profit whole value mode on production & supply sales; both tracks the optimization of branch workshop cost sensitive index and highlights business value of functional departments, establishing proficiency assessment and emphasizing “measurable, verifiable, launchable and shareable”; comprehensive and measurable multi indexes, index completion rate of security, production, consumption and recovery rate for production workshop, as well as the targeted “major business index” for each functional department, taking monthly raw material purchasing completion rate of sales & marketing department, monthly budget profit completion rate and financial expenses rate, as well as occupation of value-added tax rebates of financial department as an example, these are all based on annually/monthly production &supply sale plan and budget as assessment benchmark. Employee’s merit pay is related with completion rate, which can be realized per month.
2. Problem oriented, crux focused, exact target at management; establish and complete the budget performance assessment whole value process. After deciding profit mode, in the real operation process of advancing quality and efficiency, CCS focused on enterprise major risk point and benefit “loss point” with “problem-oriented thinking”, setting bottom line, defining red line, comprehensively managing security, marketing and finance process and implementing “benchmarking management”: benchmark homogeneity index with leading index both in China and abroad; benchmark non-homogeneity index with its best level in history; find out the gap, establish goals and make continuous improvement! CCS encourages departments and branch workshops to combine benchmarking management result with information technology, make in time summarization, solidify and realize the transformation from “tacit knowledge” to “explicit knowledge”; CCS carries out budget performance assessment system under the guidance of capital & profit whole value mode on production & supply sales; both tracks the optimization of branch workshop cost sensitive index and highlights business value of functional departments, establishing proficiency assessment and emphasizing “measurable, verifiable, launchable and shareable”; comprehensive and measurable multi indexes, index completion rate of security, production, consumption and recovery rate for production workshop, as well as the targeted “major business index” for each functional department, taking monthly raw material purchasing completion rate of sales & marketing department, monthly budget profit completion rate and financial expenses rate, as well as occupation of value-added tax rebates of financial department as an example, these are all based on annually/monthly production &supply sale plan and budget as assessment benchmark. Employee’s merit pay is related with completion rate, which can be realized per month.
Since early 2016, employees suddenly found out that the former “short and small” monthly salary sheet turned much longer. Except for the remained original content, there were more things as follows: current month cost completion performance coefficient, current month quota material completion coefficient, current month budget profit completion coefficient, current month department index completion coefficient, localization assessment completion coefficient. Moreover, the calculated rewards or fine money for each corresponding coefficient were right behind them. Some frowned and fell into deep thought, some sighed with regret that “I was so close!”; some yelled excitedly that “I will work harder next month”. Each employee work in calculation and learn during work, which has gained an fruitful result.
3. Billboard management, daily clearance and balance, rapid accomplishment for those who accumulate from tiny points“Why oxygen dumping ratio is so high”, asked by Fan Wei, executive director and CCS general manager right in front of the screen of CCS master control room when looking at an index with red light few days in a row. Before 2016, CCS did not exist oxygen dumping ratio index, which was newly added after implementing “billboard management” for quality and efficiency advancing.
3. Billboard management, daily clearance and balance, rapid accomplishment for those who accumulate from tiny points“Why oxygen dumping ratio is so high”, asked by Fan Wei, executive director and CCS general manager right in front of the screen of CCS master control room when looking at an index with red light few days in a row. Before 2016, CCS did not exist oxygen dumping ratio index, which was newly added after implementing “billboard management” for quality and efficiency advancing.
Influent engagement between each workshop section, unmatched converter production with ISA furnace used oxygen lead to empty oxygen with converter and shaking furnace, analyzed by Wang Sen, director of production department.
Zhu Shiwei, factory director of power branch said “we can automatically control ISA furnace improving blanking quantity to balance oxygen supply when using converter and shaking furnace through DCS system communication”.
Yan Jun, factory director of smelting branch added “ we can regulate and control the oxygen balance through management method before DCS configuration transformation completed”.
“Increase blanking quantity by 3t/h when using converter and shaking furnace ”, “Converter recovers oxygen for stable pipeline oxygen pressure”. Rapid linkage between gas workshop and smelting branch factory followed by each clear orders from master control room.
“Increase blanking quantity by 3t/h when using converter and shaking furnace ”, “Converter recovers oxygen for stable pipeline oxygen pressure”. Rapid linkage between gas workshop and smelting branch factory followed by each clear orders from master control room.
Finally, hard work was paid off. Oxygen dumping ration decreased to 5% in April from 10.2% in January 2016. However, dispatcher from master control room did not relax for “completion index” for oxygen dumping ratio on the screen was still yellow, and “plan index” showed clearly oxygen dumping ratio was 4%, which was their index.
“Month can not surpass day, quarter can not surpass month and year can not surpass month. If we can work on tiny things everyday, then we can achieve a lot through days of accumulation; however, we can not again a lot from big deals for they are not coming everyday. That’s why we appreciate the accumulation from tiny things in our daily life, which can lead to rapid success”. The company promotes “daily clearance and balance billboard management” system, making clearly the former day completion information and difference between monthly plan for more than 20 key indexes; uses 15 minutes of morning meeting, researching and solving red light index and tracking & focusing on yellow index, to ensure the completion and control of each measure of quality and efficiency advancing.
4. Core leadership, same purpose between leaders and subordinates, full play to the powerful guarantee role from overseas Party construction and ideological & political work to explore a path for quality and efficiency advancing in competition benefit mode As a central government overseas company, CCS leader group always gives full play to the fighting force and leading role of Party construction and ideological & political work in terms of enterprise overcoming difficulties, exploration and innovation as well as quality & efficiency advancing. Therefore, under the circumstance of overseas busy work, shortage of working staff and many floating Party members, first of all, CCS strictly obeys Party organizational life system during busy work schedule, continually improves leading Party cadres principle awareness, policy awareness, overall situation awareness, core value awareness, emulation awareness, as well as serving the country by sacrificing overseas resources with practice through earnestly learning Party lines, principles & policies, the 18th National People’s Congress Report, and themes of general secretary Xi Jinping speeches. CCS Party committee carries out learning system by middle level cadre and above: in addition to the self-learning specified documents, there should be at least mass learning per month in terms of central government or upper level organization one of the recent important documents, one lesson given by a member of the leading group, one lesson given by a middle level cadre with careful preparation of courseware with monitoring & comments; secondly, combining the promotion of Party construction conduct with anti-corruption work, CCS balances each level of authority powers among leading group members to restrict an supervise each other; constantly establish and complete full authority and supervision systems to promote scientific and democratic decision-making mechanism and completely eradicate corruption, forming righteous and clean political and operational environment. Improve staff cohesion by developing democracy, transparency & honesty. For decision-making of company affairs, especially “ Three-Importances & One-Large" matters, CCS needs to finish initial plan based on opinion poll and specific objective condition, under the condition of protection for staff basic rights and interests, and carries it out after full discussion and decision by manager office will; thirdly, improve ideological & political work and team construction of leaders and staff. Setting “index proposal, talent development, value creation and emerging brain cultivation” as core principle, to rapid the pace of inner unity between leadership development and the realization of current major production & operation target. CCS also highlights the development of local employees while giving full play to Chinese employees to actively promote localization management. “Success goes for the same purpose between leaders and subordinates”. Different from domestic companies, all Chinese employees are far apart from China and their hometowns, bringing difficulties to ideological & political work. CCS has done a lot in this field, creating people-oriented family and friend working relationship. For a long time, all CCS employees have always been creating a sound atmosphere “resource serving the country dream” with personal ambition in real life and family happiness dream even they are far apart from homelands and families no matter in in capital building period or in production period. In daily work & life, CCS employee and corporate value has been gradually established—“dedication, concentration and service”, exerting and arousing subjective initiative of mass leaders in the process of company production, operation and construction.
4. Core leadership, same purpose between leaders and subordinates, full play to the powerful guarantee role from overseas Party construction and ideological & political work to explore a path for quality and efficiency advancing in competition benefit mode As a central government overseas company, CCS leader group always gives full play to the fighting force and leading role of Party construction and ideological & political work in terms of enterprise overcoming difficulties, exploration and innovation as well as quality & efficiency advancing. Therefore, under the circumstance of overseas busy work, shortage of working staff and many floating Party members, first of all, CCS strictly obeys Party organizational life system during busy work schedule, continually improves leading Party cadres principle awareness, policy awareness, overall situation awareness, core value awareness, emulation awareness, as well as serving the country by sacrificing overseas resources with practice through earnestly learning Party lines, principles & policies, the 18th National People’s Congress Report, and themes of general secretary Xi Jinping speeches. CCS Party committee carries out learning system by middle level cadre and above: in addition to the self-learning specified documents, there should be at least mass learning per month in terms of central government or upper level organization one of the recent important documents, one lesson given by a member of the leading group, one lesson given by a middle level cadre with careful preparation of courseware with monitoring & comments; secondly, combining the promotion of Party construction conduct with anti-corruption work, CCS balances each level of authority powers among leading group members to restrict an supervise each other; constantly establish and complete full authority and supervision systems to promote scientific and democratic decision-making mechanism and completely eradicate corruption, forming righteous and clean political and operational environment. Improve staff cohesion by developing democracy, transparency & honesty. For decision-making of company affairs, especially “ Three-Importances & One-Large" matters, CCS needs to finish initial plan based on opinion poll and specific objective condition, under the condition of protection for staff basic rights and interests, and carries it out after full discussion and decision by manager office will; thirdly, improve ideological & political work and team construction of leaders and staff. Setting “index proposal, talent development, value creation and emerging brain cultivation” as core principle, to rapid the pace of inner unity between leadership development and the realization of current major production & operation target. CCS also highlights the development of local employees while giving full play to Chinese employees to actively promote localization management. “Success goes for the same purpose between leaders and subordinates”. Different from domestic companies, all Chinese employees are far apart from China and their hometowns, bringing difficulties to ideological & political work. CCS has done a lot in this field, creating people-oriented family and friend working relationship. For a long time, all CCS employees have always been creating a sound atmosphere “resource serving the country dream” with personal ambition in real life and family happiness dream even they are far apart from homelands and families no matter in in capital building period or in production period. In daily work & life, CCS employee and corporate value has been gradually established—“dedication, concentration and service”, exerting and arousing subjective initiative of mass leaders in the process of company production, operation and construction.
Be prepared for danger in times of safety; be prepared for changes in times of danger. CCS management team fully realized that: the tough period of non-ferrous metals industry is also a very good opportunity for realizing “rising through difficulties” by advancing quality and efficiency, making the gap between competitors to ensure regional competition advantage, also a golden window period to plan and launch development reserve projects. A road of a thousand miles begins with one step. To vigorously realize 2016 annual production and operation target by advancing quality and efficiency is not only the task requirements of the current year, but also key supporting factor to lay foundation for company development during the 13th Five Year Plan Period. CCS leader group and all working staff know time and tide wait for no man and decide to burden more pressure from themselves, striving for extra 10 million us dollars based on profit indicator issued early this year, planning for the whole year production and operation. At the same time, CCS needs not only production and profit, but talents, to provide strong human resource for oversea strategic expanding.
As of press time, CCS excessed the production plan this year from January to April; blister copper unit energy consumption is 130 kg of standard coal/ ton copper, decreased by 26% compared with 2015; copper slag flotation variable cost decreased by 16% compared with 2015. CCS is on the way of quality and efficiency advancing.
As of press time, CCS excessed the production plan this year from January to April; blister copper unit energy consumption is 130 kg of standard coal/ ton copper, decreased by 26% compared with 2015; copper slag flotation variable cost decreased by 16% compared with 2015. CCS is on the way of quality and efficiency advancing.
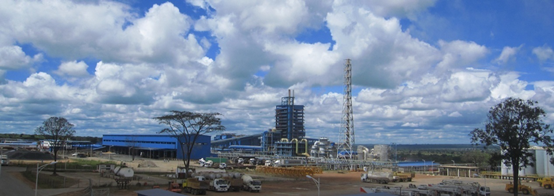
CCS modernized factory under blue sky and white cloud
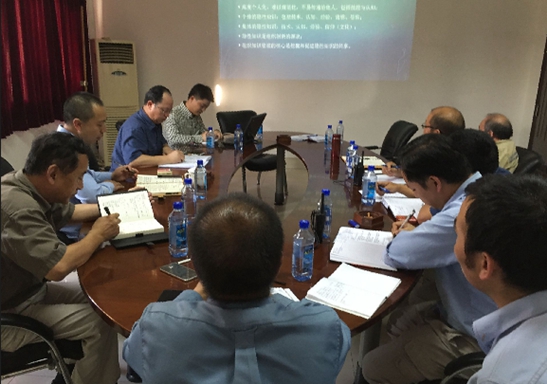
Massed learning for middle level leaders and above
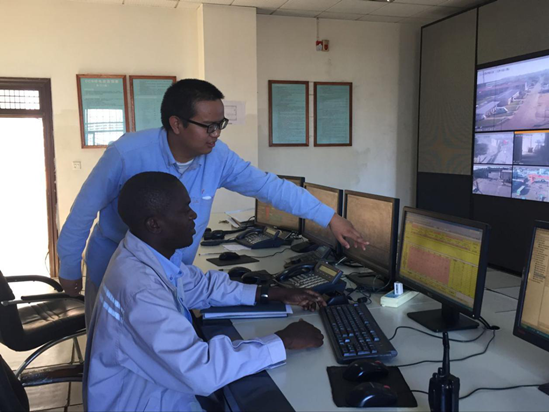
Chinese employee is helping local employee.
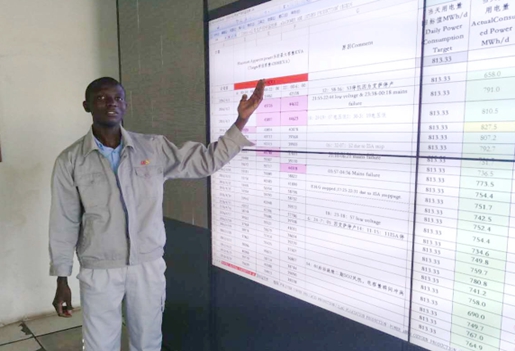
Employees from China and Zambia both are promoting “billboard management, daily clearance and balance system”.
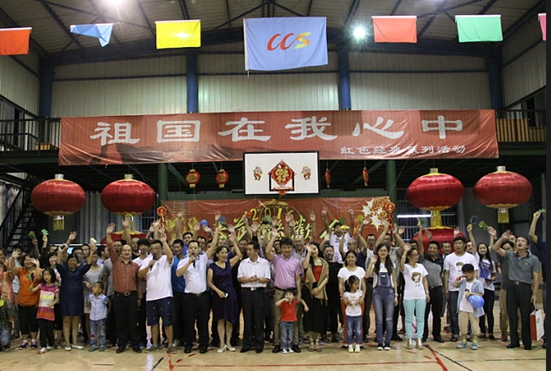
CCS leader group is celebrating Chinese Lunar New Year with Chinese employees.
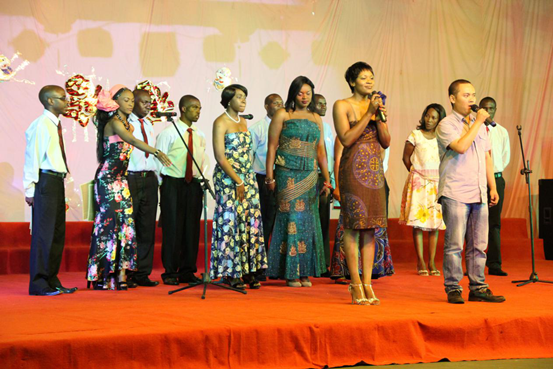
Chinese and Zambian employees are celebrating New Year together.
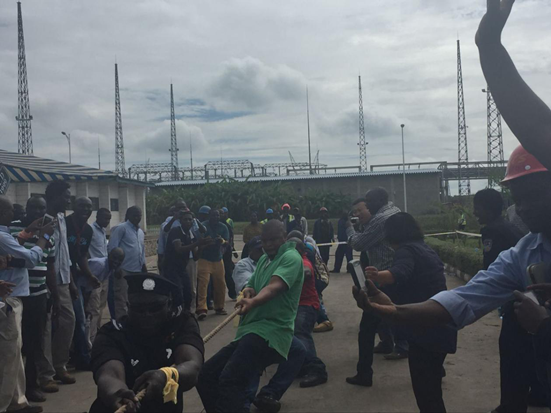
Tug-of-war competition at Christmas
News Center
Breaking news
China Nonferrous Mining Corporation Limited Successfully Implements Lightning Equity Placement, Raising HK$978 Million
23 May 2016
The Company Successfully Holds the 4th Regular Board Meeting for 2023
23 May 2016
The Company Successfully Holds the 3rd Regular Board Meeting for 2023
23 May 2016
The Company Holds Annual Shareholders' Special Meeting for 2023
23 May 2016
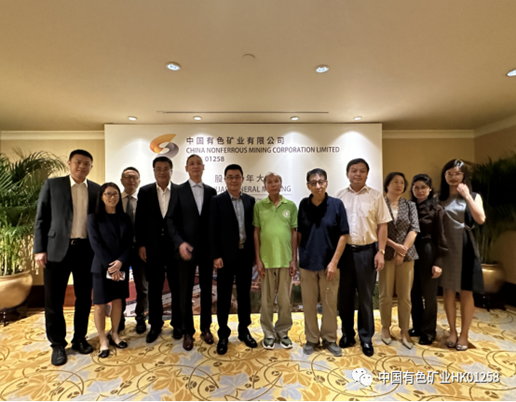
China Nonferrous Mining Corporation Limited Annual General Meeting Held in Hong Kong
23 May 2016